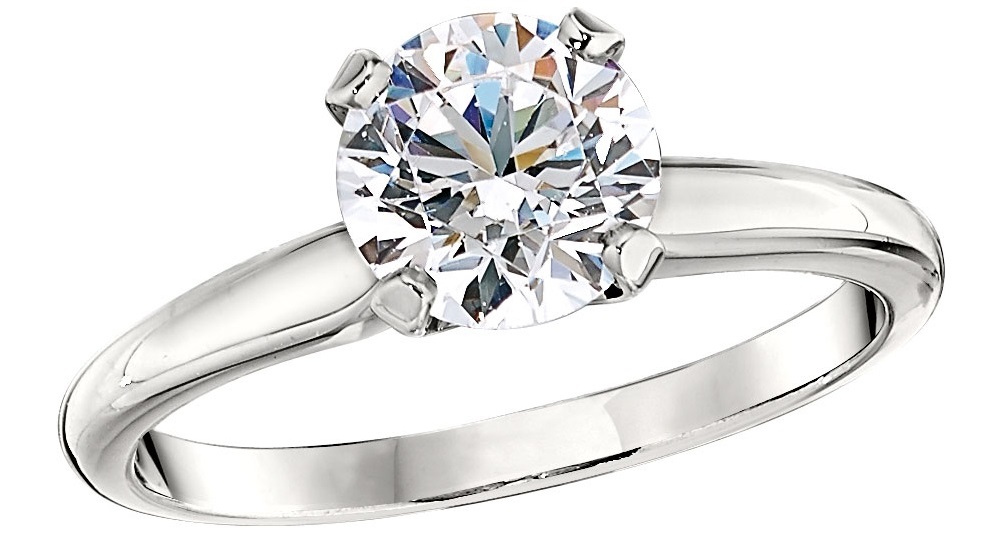
While a Jabel classic solitaire may look like a simple ring setting, it is truly a work of art! Making our die struck engagement ring settings is both a labor of love and an engineering work of art. A closer look into its production offers a glimpse into Jabel's dedication to quality and our strict attention to detail.Step 1: Making The MetalThe process begins with our own signature recipe for alloying gold, where a time honored proportion of karat and fine alloys are blended to create each of Jabel's exquisitely colored metals including yellow, white, rose, and green gold! Our ingots, which is the name of the gold that is produced in the alloy process, is then rolled under extremely heavy pressure to form non-porous, solid and homogeneous “ribbons” of metal in various desired thicknesses, depending on the style being produced. The ribbons are then cut to the proper size for the chosen mounting.Step 2: Die StrikingThe metal is now ready for die striking. Using our steel dies the desired piece is “blanked out” of the gold ribbons, then repeatedly and alternately struck with fifty tons of pressure and heat treated; also called annealed, to achieve malleability, which minimizes potential cracks in the metal. After the initial strike the overflow of metal is trimmed with a pressure strike, the part is annealed and struck with a “finish” trim.
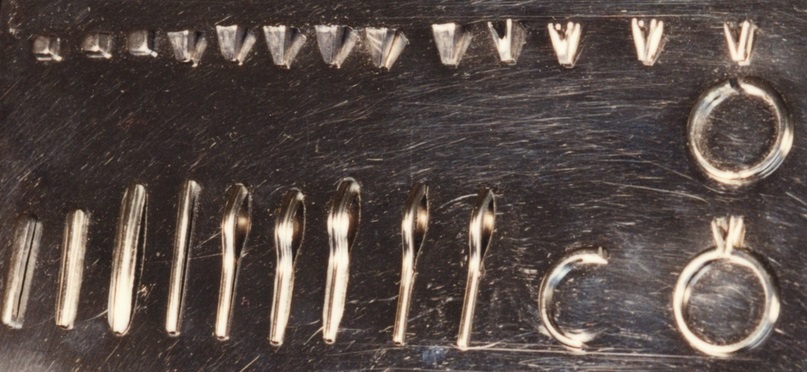
Step 3: ShapingThe process as described above applies to both the mounting's shank and the chosen crown (also called a setting or head). The shank is struck, flat, in one piece or in half-shanks depending on the needed finger size. The shank/half shanks is then rounded-up using a manual machine.Step 4: JewelersThe parts are now given to a bench jeweler for assembly. Assembly includes filing the parts for proper fitting of angles and such, soldering the parts together using the proper karat gold solder, for our 18KW we use 20 karat hard solder which requires a temperature of approximately 1600 degrees Fahrenheit, pickling which is a low acidic solution used for cleaning the soldered areas, then a final cleaning of the entire mounting with emery paper.Step 5: PolishingThe mounting is then taken to the Polishing Department for a process called lapping. Lapping removes the minute rough marks in the metal resulting from jewelers filing and also shapes the piece. A compound is applied to felt wheels, of which there various hardness, sizes and shapes and the polisher uses eye-hand coordination as well as professional ”touch” to accomplish desired results.Step 6: FinishingThe Jabel trademark is manually stamped inside the shank along with the karat gold or platinum stamp. Then the piece is sent to finishing where a high, bright finish is applied with a series of soft buffing wheels. Next, the ring is cleaned with an ammonia based detergent in an ultrasonic tank. Once out of the tank the mounting is steamed and air-blown dry. Yellow gold mountings are now ready for final inspection; white gold mountings are rhodium plated to further whiten the piece especially the solder joints prior to final inspection.Step 7: InspectionWhile a final inspection is always performed on every piece of Jabel jewelry. However, what many people do not know is that our team of dedicated artisans conduct inspection at the beginning and end at each stage of production. They take pride in creating exceptional jewelry.Bonus Info: Hand EngravingDid you know that Jabel's die struck ring are the perfect canvas for hand engraving? Yes, our hand engraved jewelry is created by our expert engraver who uses skill, superb hand-eye coordination, and a dedication to perfection to bring exceptional artistry to our jewelry. To learn more about the process read this article.
Email us to find a local Jabel jeweler at info@jabel.com